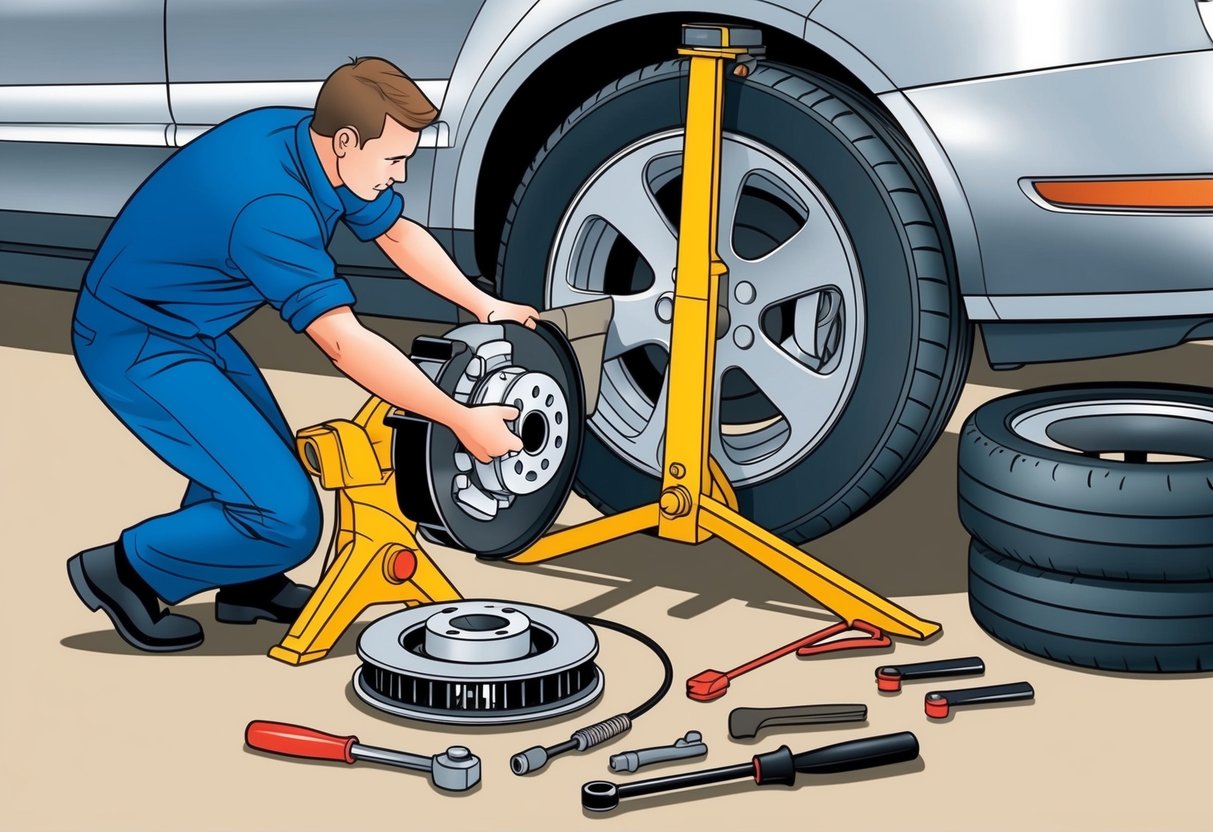
Essential Tools and Safety Precautions
Proper tools and careful safety measures are critical for anyone performing a brake job at home. The correct gear not only makes the brake service process more efficient but also reduces risk of injury and helps ensure the repairs are completed within legal safety standards.
Tools for DIY Brake Repair
A successful brake pad or rotor replacement requires several essential tools. The basics include a car jack, jack stands, and a lug wrench to safely lift and secure the vehicle.
A socket set with ratchet, ideally both standard and metric sizes, is needed to remove caliper bolts and other hardware. Other important items are pliers, a C-clamp or brake caliper tool for retracting the caliper piston, and a flathead screwdriver for prying.
Use brake cleaner to remove built-up dust or grease. A wire brush helps clean rust and debris from hardware.
For a more comprehensive list, see this detailed brake repair guide. Shop towels and a drip pan make clean-up easier and help manage brake fluid spills.
Quality brake lubricant is important for moving parts and pins. In some cases, a torque wrench is needed to ensure bolts are tightened to manufacturer recommendations.
Safety Gear and Workspace Setup
Before starting any brake job, safety takes priority. Use mechanic’s gloves for hand protection, as brake components can have sharp edges.
Safety glasses guard against dirt, rust, or debris during disassembly and cleaning. A well-lit, flat, and stable workspace is essential.
Always use jack stands—never rely solely on a car jack—to support the vehicle once it is lifted. Wheel chocks prevent unwanted rolling and keep the car secure.
Proper ventilation is necessary, especially when using brake cleaner or working with brake dust. Keep a fire extinguisher nearby and ensure tools are organized to avoid tripping.
These practices help create a safe, efficient environment for any at-home brake service or repair. For more on workspace preparation and specific safety priorities, visit this DIY safety guide.
Preparing for Brake Inspection
Before starting any brake inspection or repair work, gathering the right tools and ensuring a safe workspace is essential. By carefully lifting the vehicle and completing a thorough initial assessment, owners can identify potential issues with the brake assembly and decide on the next repair steps with confidence.
Vehicle Lifting and Wheel Removal
Properly lifting the vehicle is critical for a thorough brake inspection. Start by parking on a flat, solid surface, and always apply the parking brake.
Use wheel chocks on the wheels that will remain on the ground to prevent any movement. A hydraulic floor jack should be positioned at the manufacturer’s recommended lift points.
Once the vehicle is raised and secured with jack stands, double-check the stability before loosening any wheel lug nuts. Removing the wheel exposes the brake assembly, including the caliper, rotor, and pads.
For safety, never rely solely on a jack to support the vehicle. Reference the owner’s manual to locate appropriate lift points and recommended tools.
Accurate lifting and secure wheel removal set the stage for a focused brake inspection, minimizing risk of injury or damage.
Initial Brake Assembly Assessment
Begin the brake inspection by closely examining the brake assembly components. Inspect the brake pads for uneven wear, thinning, or any embedded debris.
If the friction material is 3mm thick or less, replacement is recommended. Look for scoring, grooves, or discoloration on the brake rotor surface, which may indicate overheating or wear.
Spin the rotor by hand to detect resistance or unusual noises, which may signal worn bearings or rotor warping. Check calipers for leaks, cracks, or visible corrosion.
Test the brake fluid level at the reservoir and check its clarity. Cloudy or dark fluid suggests contamination.
For more details on contamination signs, see this car owner’s guide to brake repair. Accurate assessment of the brake assembly at regular mileage intervals can prevent more costly repairs and ensure safe vehicle operation.
How to Inspect Brake Components
Performing a thorough inspection of brake parts is essential for safe and reliable vehicle operation. Identifying issues with pads, rotors, calipers, and slides early can prevent more severe damage and costly repairs.
Examining Brake Pads and Shoes
Begin by removing each wheel to clearly access the brakes. Inspect the brake pads for thickness—if the friction material is 3mm or less, it is time to replace the pads.
Uneven wear or tapered pads may indicate problems such as misaligned calipers or worn hardware in the brake system. Check for deep grooves or cracks on the surface of both brake pads and brake shoes.
Pads should be free of glazing, which appears as a shiny, hardened surface and can reduce stopping power. Take note of any embedded debris or oil, as contaminated friction material cannot safely stop the vehicle.
Check the brake pad set to confirm that all pads are wearing evenly. For drum brake systems, the brake shoes should have uniform lining and no significant wear lip.
If the shoes are less than 2mm thick at any point or show signs of shedding material, they should be replaced.
Checking Rotors and Drums
Rotor and drum inspection is critical for identifying issues that cause noise and vibration. Look at the brake rotors and drums for any scoring, grooves, or heat spots.
Surface rust is normal, but heavy pitting or a blue or purple discoloration means the rotor has overheated and may be warped or weakened. Run a fingertip along the rotor edge to feel for a pronounced wear lip—a raised ridge around the outer edge.
A significant lip often means the rotor is below the minimum thickness. Thin or tapered rotors compromise braking performance and should be replaced.
Measuring the rotor thickness with a micrometer and comparing it to manufacturer specifications is the best way to ensure safety. For drums, inspect the inside surface for deep grooves or cracking.
Any out-of-round or egg-shaped drum is unsafe. Drums and rotors that are excessively worn or damaged should be replaced rather than resurfaced.
Learn more about how to inspect the rotor and replace it if needed.
Assessing Calipers, Brackets, and Slides
The caliper assembly should be checked for leaks, seized pistons, or tearing around the dust boots. Damaged pistons can lead to dragging or uneven brake wear.
Pay particular attention to caliper brackets and slide pins, which allow the caliper to move freely as the brakes engage. Remove the slide pins and inspect for rust, pitting, or a lack of lubrication.
Clean pins and bores thoroughly, then apply a thin layer of high-temperature brake grease to the slides before reinstalling. Sticking or seized components should be repaired or replaced immediately to avoid accelerated pad deterioration and unsafe braking.
Hardware such as anti-rattle clips and pad retainers must also be checked for corrosion, fatigue, or loss of tension. Replace any worn hardware for proper caliper operation and pad alignment.
A step-by-step guide is available on how to lube and inspect brake slides and brackets for best results.